Sinking Concrete Solved in the Kansas City Metro & Mid-Missouri: Exploring the Benefits of Polyjacking
Sinking and shifting on concrete slabs like sideways, driveways, or garages are quite common. There are many different types of solutions available for lifting up and repairing the concrete elements. Among them, the most recent and popular method is the polyjacking method. Kansas City and mid-Missouri‘s experts, PolyMagic, are equipped to lift and level your uneven concrete within minutes.
The benefits of this method are greater than those of mudjacking, which is the traditional (older) method. If you’re thinking about solving sinking concrete problems on your property, you should know all the fundamentals of this method for the best experience. In this article, we’ve briefed about the polyjacking method. Let’s learn about it, so homeowners can understand how this is the best solution for repairing vs replacing your home’s concrete.
WHY DOES CONCRETE SINK?
Concrete is a composite material that includes different aggregates like sand, stones, gravel, cementitious material, and water in specific ratios. All the materials are mixed and molded together to form a durable, high-density composition.
As the concrete is so dense, it quickly sinks into liquids. But in loose solids, like sand or clay, a concrete element will sink slowly. For hard surfaces, like solid grounds, the concrete materials don’t sink or settle easily, specifically if the applied load isn’t too high.
However, heavy or large concrete elements like sidewalks, pathways, foundations, etc. can even sink where the ground is supposed to be solid enough to keep them level. There are several reasons why this can happen, for example:
- If the concrete structure or element is poorly made with weak materials or has an inadequate ratio of aggregates and reinforcement.
- In case the soil isn’t compacted properly, loose soil can make the concrete settle unevenly over time.
- If the soil beneath the concrete erodes off due to weather or other effects, it can form voids and make the concrete sink.
- In case the water amount in the ground below the concrete element increases, it’ll lead to water accumulation under the concrete, make the soil unstable, and lead to concrete settlement.
Sometimes components of tree roots decompose and make voids in the ground, which can lead to concrete settlement.
WHAT IS POLYJACKING?
Polyjacking goes by different names including ‘poly leveling’ and ‘foam leveling’. This is a recently invented method for concrete leveling where liquid foam is injected inside voids of concrete or under the concrete slabs to fill the gaps, make the concrete level, and make things more stable. The chemical properties of the foam make it expand and solidify after being injected, making it suited for void fillings.
RELATED: Polyurethane foam: A Smart Solution for Concrete Lifting
BENEFITS OF POLYJACKING
There are various benefits to using polyjacking to lift up sinking concrete. The most significant benefits are:
- Polyjacking ensures a quick repair within a single day. You can even finish all the work and start using the area after a few hours.
- It’s a cost-effective solution for small to mid-level problems.
- Polyjacking provides a long-lasting result compared to other methods.
- This process isn’t as hassling as other methods. It has minimal interference with its surroundings.
- The amount and entire process are adjustable according to needs.
- Since the equipment and polyurethane foam are so lightweight, it’s easy to carry and work anywhere.
- Polyurethane foam is resistant to chemicals, water, moisture, and other environmental factors.
STEPS OF THE POLYJACKING PROCESS
We can divide the polyjacking process into several steps to understand them easily and apply them effectively. The steps are:
IDENTIFYING ISSUE
The very first step is to identify the issue of concrete sinking. If the reason is something to do with soil or a void, it can be solved with the polyjacking method. But if the concrete is breaking apart and sinking, there can be structural issues, and you may need to recast concrete, or sometimes both. So make sure why the problem is happening.
INSPECTION
After you identify the issue and decide to use the polyjacking method, you need to do an overall inspection. You should hire a contractor with polyjacking experience and licenses and ask them to inspect the site. They can give you a rough estimation of how much time or foam is required for the process and how much it can cost after their inspection. Even they can suggest better or extra service depending on the situation they assess.
PREPARATION
When you and the contractor decide on the time to do polyjacking, the next step is preparation. You should clean the concrete and surrounding area to get rid of any debris. Also, ensure that no one will have to use that area while the polyjacking process continues. You can also take some safety precautions about it. Also, prepare the area where the equipment will be stocked temporarily.
DRILLING AND INJECTING FOAM
Now the contractor will start the main process. They will drill very small holes in the concrete slabs at specific distances and start to inject polyurethane foam through the holes. The foam will fill the voids, start solidifying after some time, and lift the concrete panels.
MONITORING AND ADJUSTMENT
While doing the polyjacking process, real-time continuous monitoring should be done. Depending on the situation, you’ll need to adjust the injection amount of foam or drill more holes and fill other areas. Also, the lifting process can be uneven, so everyone should closely monitor the process.
COMPLETION
Now it’s time to complete the polyjacking process. Ensure the slabs are properly leveled, and if you see any part is a bit down, inject foam there immediately. Once you’ve confirmed everything is alright, you can fill the holes using mortar.
CLEAN-UPS
Clean up excess foam and mortar from the concrete and remove all the equipment from the surrounding area.
CURING
You need to let the concrete and foam cure for a few hours. Ensure no load is applied to the concrete during that time.
Polyjacking is definitely a popular and effective method for repairing and leveling concrete elements. However, there are some cases where polyjacking isn’t the best or long-lasting solution; you may need underpinning, mudjacking, or all three. Only a skilled or experienced professional will determine what method is best suited for your problem; that’s why you should hire one and follow their instructions properly.
If you’d like to request a free estimate, fill out this form or call (816) 451-4535 (Kansas City) or (573) 496-8146 (Jefferson City or Columbia area).
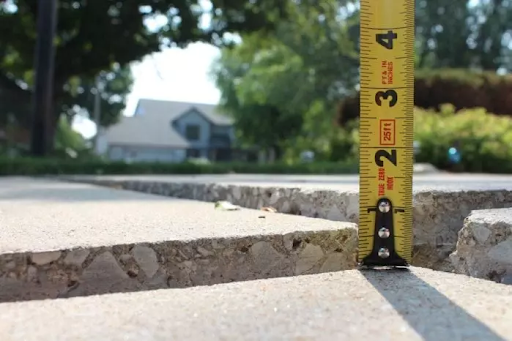
Sinking Driveway in the Kansas City Metro & Mid-Missouri: Should You Repair or Replace the Concrete?
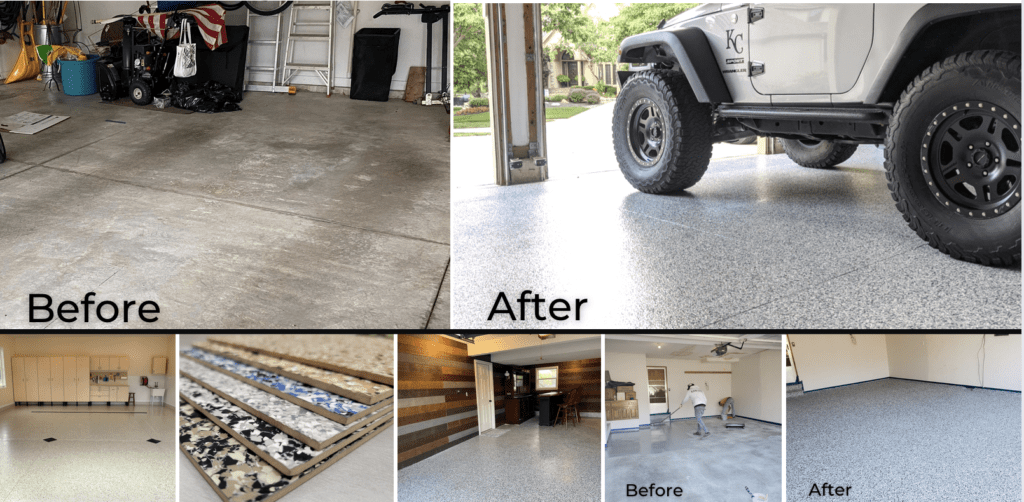